In the To-Syn-Fuel plant, sewage sludge is converted in Fraunhofers Thermo-catalytic reforming (TCR) system into valuable solid, liquid and gas fractions. The produced liquid bio-oil is refined to suitable fuels using the hydrogen from the produced TCR gas fraction. This hydrogen will need to be purified first. Hydrogen is separated from other species, like carbon monoxide, carbon dioxide and methane using one of project partner HyGear’s key technologies: Pressure Swing Adsorption (PSA). The separation is based on variation of adsorption capacity of an adsorbent as function of operating pressure. The cleaned hydrogen is compressed and redirected to the hydrodeoxygenation (HDO) reactors or can be used for other applications, like fuel cells. The required purity of the hydrogen can be controlled by the PSA settings.
The existing PSA technology has been modified to meet the specification of the TCR gas combined with recycled hydrogen out of the HDO part of the TSF plant. Several technology improvements have been implemented to reduce size and cost of the PSA.
The hardware has been designed and assembled at HyGear in Arnhem, The Netherlands. The PSA is fully automated and can run safely without human interference. The system is CE certified and installed in a container for easy handling and for in- and outdoor use.
Mid June 2020, the PSA the construction was finalized, the software loaded and the container ready for shipment to the To-Syn-Fuel plant in Hohenburg in Bavaria, Germany. The system will be installed during the summer. The commissioning phase will start in September and first gas will be cleaned by the end of this year.
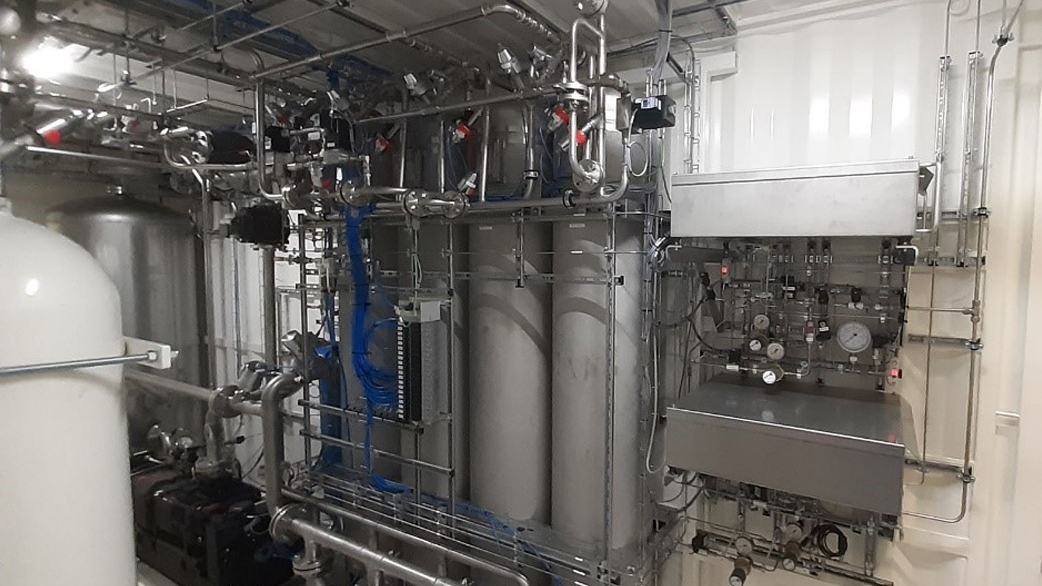
Figure 1: installed To-Syn-Fuel PSA
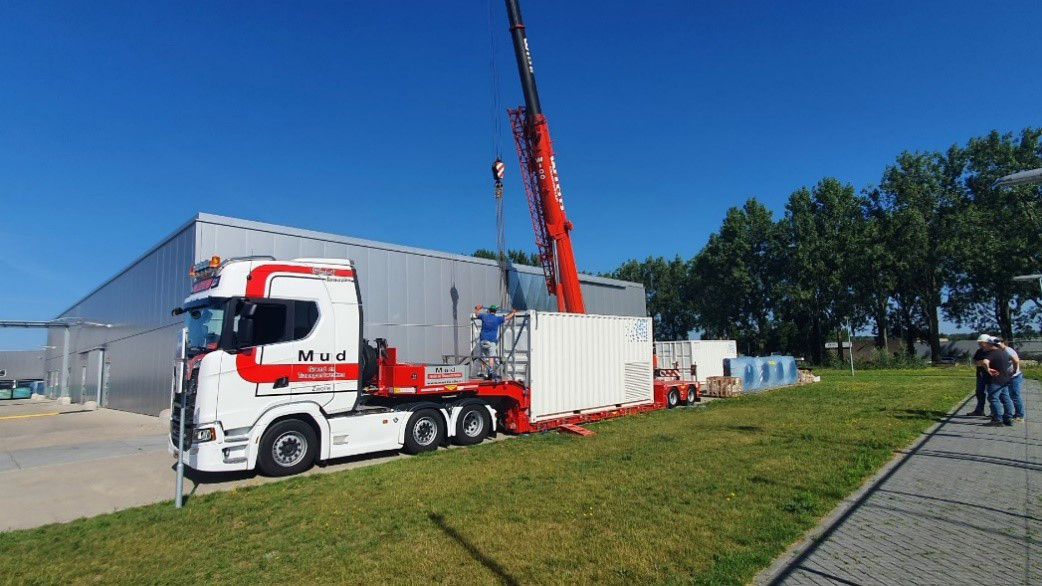
Figure 2: To-Syn-Fuel PSA ready for shipment